Aline Eid receives MTRAC Award to commercialize radar vision for autonomous indoor navigation

Aline Eid has been awarded a grant from the Michigan Translational Research and Commercialization (MTRAC) Advanced Transportation Innovation Hub to support her research on radar vision for autonomous robots and drones. The technologies she develops will be marketed in collaboration with the startup Atheraxon in an $8B serviceable market for autonomous guided vehicles (AGVs).
Many warehouse tasks are good candidates for automation, due to monotony or hazardous conditions for human workers. A large majority of supply chain professionals view warehouse automation as a positive innovation for the industry, with 75–77% of organizations planning to automate some of their warehouse processes in the next three years [source]. However, as of 2021, only 6% of warehouses had deployed AGVs due to financial or logistical limitations.
“It is incredibly difficult for automated systems to precisely locate themselves in space,” said Eid. “This multi-billion-dollar problem is stifling the growth potential of hundreds of industrial robotics companies by setting the starting cost of their robots above tens of thousands of dollars per unit and limiting their appeal to niche markets.”
Robots must have an accurate, constantly updating map of both their surroundings and their position in space. The current state-of-the-art methods use Light Detection And
Ranging (lidar) to sense the distance and shape of objects in a robot’s surroundings with a spinning laser; the scans are then fed into a Simultaneous Localization and Mapping (SLAM) algorithm, which maps a 3D representation of the environment and determines the relative location of the robot.
However, this combination of lidar and SLAM can be prohibitively expensive, computationally intensive, and fails in very dynamic situations. A typical warehouse, with its many mobile workers and flexible layout challenges the abilities of lidar SLAM.
Eid has developed a solution that overcomes these challenges using radars that are specifically programmed and tuned to detect and accurately locate fixed and mobile landmarks in the environment. This solution saves computational power, is cost effective, and improves on human labor options in dull or dangerous conditions.
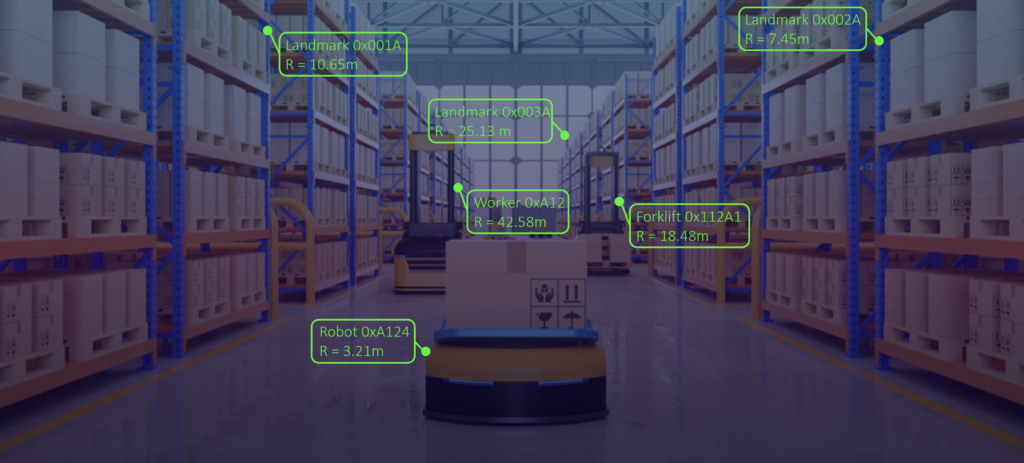
“Our solution introduces a radar technology to the robotics space that enables a 10X lower cost and fully dependable new solution to this problem,” Eid said. “The very first introduction of this new and cutting-edge radar technology to the robotics space has the potential to radically enhance the abilities of rolling, walking, and flying robotics platforms in indoor facilities.”
Eid’s team will sell the patented technology and process—including the radar module and a SLAM algorithm for the radar equipment—to companies that design and manufacture AGV robots as a customized solution.
The technology can help automate tasks such as forklift operation, inventory, loading and unloading pallets or conveyer belts, and transporting items throughout the warehouse. Automating these tasks allows them to be done more quickly and reduces error, while keeping human workers safe from falls and injuries. Together, these benefits can make global supply chains more stable, efficient, and reliable.
Eid will be doing this work with Skanda Harisha, an ECE PhD student in Eid’s research group. In addition to the financial support from MTRAC, the team will receive “commercialization resources and support, including connections to industry partners, coaching and mentoring from the MTRAC team, and access to an industry and venture capital advisory board.”
By August 2025, the team plans to have completed a successful demo of the technology in a complicated industrial environment. By 2027, they hope to have the new system marketed and deployed at scale to companies.